
Asset Management in the heavy industry with RFID!
Nothing gets lost!
Quick inventory / counting and monitoring of tools and machine parts during service and maintenance work with RFID.
A daily challenge for both small and large companies. Always the same problem. Service or maintenance work has to be carried out.
A precisely timed implementation is required to ensure that downtimes are kept to a minimum.
This on the one hand, while at the same time the specified maintenance and the replacement of appropriate material must be carried out.
Sounds logical and simple at first, but it is far more complex and complicated than originally expected
The soltion from AGILLOX!
Step 1: Creation of a specification sheet together with the customer.
Step 2: All valuable parts are provided with RFID tags.
Step 3: All valuable parts are recorded, registered in a database with a corresponding description and possibly with the replacement value.
Step 4: Each part has an individual unique number and can therefore be "linked" to the corresponding description in the system.
Step 5: All employees who enter the site receive an RFID tag, which is stuck to their helmet, are registered and must pass through a dedicated gate to be recorded by the system.
The solution from AGILLOX Technical!
RFID gates:
There are different storage locations on the site where the relevant materials are deposited. Either the equipment is simply stored to be used again later or the equipment is sent to the workshop (repair, maintenance, overhaul, etc.). Parts that are scrapped also have their own storage location.
Each storage location therefore has a gate. Two solutions have been installed for the gates.
Gate A: The storage location has a defined entry point and another defined exit point.
Gate B: The storage location has an entry and exit point.
At each entry or exit, the tags are read and communicated to the server.
These gates were designed as fixed installations, as mobile gates or, in the highest expansion stage, as autonomous (without power supply / with solar power) mobile gates.
Mobile gates with radar and LED displays
These can be installed at any desired location at any time.
Completely equipped with RFID antenna, RFID LTE reader, switch box, radar and LED display.
Prepared to function in wind and weather.
These can be installed at any desired location at any time.
Staff gate:
A gate comes into operation here which registers both the entry and exit of employees.
A sophisticated antenna system recognizes the tags (fixed to the helmet) and identifies the direction (entrance/exit).
This means that the number of employees on the premises is known at all times.
In the event of an evacuation, a targeted search can be made for the relevant employees.
LTE RFID Reader
In addition to the challenge of designing the gates to be flexible or fixed, there was also the task of designing the data transfer in such a way that it could be transmitted from any location (without IT infrastructure).
In other words, the data had to communicate via the mobile networks. This was also one of the special features of this project.
The entire system was designed so that its function can be checked from the outside. The box has protection class IP67.
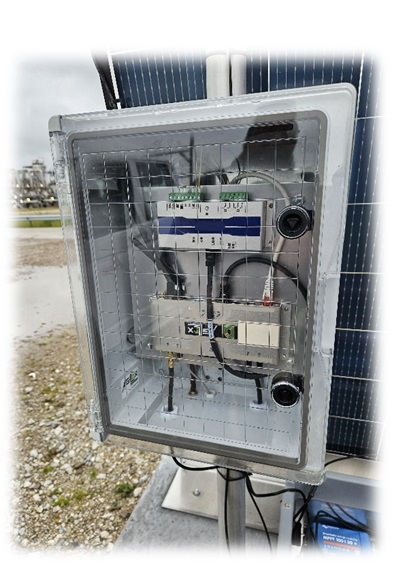
LTE RFID Reader inserted in IP67 protection box
The following processes can be carried out as soon as a sustainable reading of the equipment has been performed.
All processes required for an object, such as
- Data acquisition, both technical data and spatial information in maps and plans
- Inventory and stocktaking
- Inspection rounds and (statutory) inspections
- Damage recording and documentation
- Acceptance procedures and defect management
- Maintenance and servicing as well as incident and event management
- Provision of information and evaluations
Overview of inventory and asset management
Function overview
- Spatial allocation of fixed and movable inventory
- Storage of technical and commercial data with associated contracts, dates, events, tasks, orders, invoices, warranties, barcodes, etc.
- Document storage (e.g. warranty certificates, maintenance contracts, inspection logs, operating instructions)
- Planning, organization, execution and billing of all maintenance and servicing work
- History management
- Integration into relocation management
- Cost management (acquisition value, depreciation, condition assessment, allocation to cost centers, etc.)
- Management of specific characteristics (e.g. manufacturer, dimensions, location, warranty)
- Use of type catalogs for faster data acquisition
- Connection with CAD
- Standard evaluations
- Inventory lists (e.g. by cost center, employee, location)
- Cost overviews (acquisition, repair)
- Condition assessment
- Overviews of warranties, maintenance contracts, orders, etc.
- Inventory / stocktaking
- Maintenance, inspections, checks
- Order management
This RFID solution is scalable. This means that you start small and can easily expand it to many thousands of parts. Without additional extra effort. Whether small or large equipment, vehicles or employees.
The possibilities are "almost" endless. Virtually any part can be fitted with an RFID tag with very little effort. Regardless of the material and shape.
In addition, you can define a system in several levels and thus create badges which in turn can form subgroups. A simple structure with a great effect.
If you would like to know more about our customized solutions, simply contact us. We are a phone call or e-mail away.
AGILLOX: +31 345 623303 oder E-Mail: NLsales@agillox.com
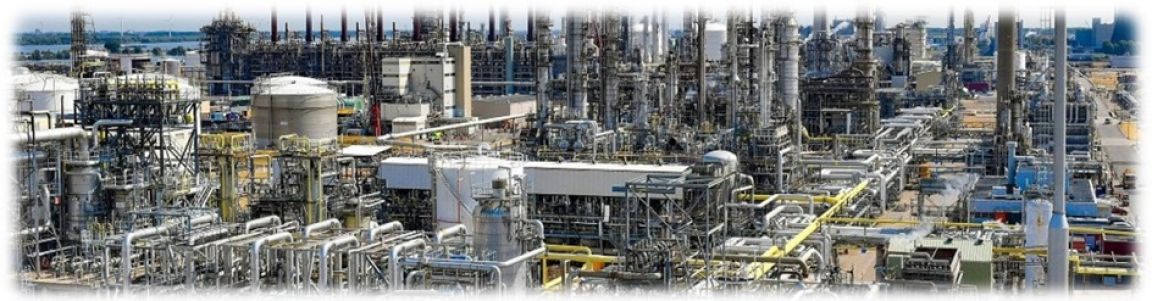
AGILLOX has developed a tailor-made solution according to the wishes and requirements of the customer, which today has no equal.
Other heavy industry companies have already expressed their interest in the same solution. We are looking forward to it.
A great project.
Your AGILLOX team